BEARING AND SEALING COMPONENTS
FOR MECHANICAL ENGINEERING
Carbon and graphite materials are a proven method for the sealing of shafts and their bearings. The special physical and mechanical properties of carbon and graphite, in particular their low coefficient of friction, hard wearing and excellent thermal resistance offer solutions to many mechanical engineering and manufacturing problems. Bearings, sealing rings and vanes made of carbon and graphite may be used for dry or wet running applications. Their use is recommended where the following conditions prevail:
- The use of hydro carbon lubricants is prevented by high operating temperatures
- Oil or other lubricating contamination must be restricted
- Chemical attack prohibits the use of other materials
- Minimum servicing requirement
- Dry running and high pressure demands a mechanically sound material with sufficient self-lubricating capability, good thermal conductivity and low coefficient of expansion
- Bearings are situated vertically or at an angle in the machine thus making lubricant retention difficult.
GENERAL APPLICATION INFORMATION
PHYSICAL AND MECHANICAL PROPERTIES
- Good dimensional stability (low thermal coefficient of expansion)
- Good heat conductivity
- Good corrosive resistance
- Good temperature resistance
- Good self-lubrication
- Good frictional characteristics
- Good machining characteristics
- Low weight
OPERATING TEMPERATURE
The temperature resistance in an oxidizing atmosphere can be specified as 500°C maximum for TYGRAF bearing qualities. In a non-oxidizing atmosphere the temperature resistance is determined by the final graphitizing treatment of each individual grade (e.g. upper application limit for graphite is approximately 3000°C). Temperature resistance is also affected by various impregnations. In the case of resin impregnation the maximum operating temperature is 180°C, for lead impregnation 200°C and antimony impregnation 500°C.
CHEMICAL RESISTANCE
Carbon and particularly graphite are characterised by excellent chemical resistance to almost all organic and inorganic media. Exceptions to this are some strongly oxidising acids, alkaline solutions, halogens and alkali molten metal.
FRICTIONAL BEHAVIOUR
Graphite has self-lubricating properties because of its crystalline structure. The low friction coefficient is a function of the low bonding between the structural lattice planes. Dislocation of one against the other is therefore easy. The friction coefficient is particularly low if traces of water or other vapours are present. The friction coefficient is greatly increased when a vacuum is created.
Because of the varying conditions of application, no exact data can be given for friction coefficients. In general the following values can be expected for sliding friction:
- dry friction 0.10… 0.30
- mixed friction 0.05 …0.10hydraulic friction 0.01 … 0.05
The frictional behaviour of carbon and graphite is also affected by the following factors:
- running in
- specific pressure
- running speed
When running in carbon and graphite bearings, the friction coefficient drops until a constant value is reached once the surfaces are smoothed.
The coefficient of friction also drops in the case of constant specific strain and increasing running speed, or at the inverse.
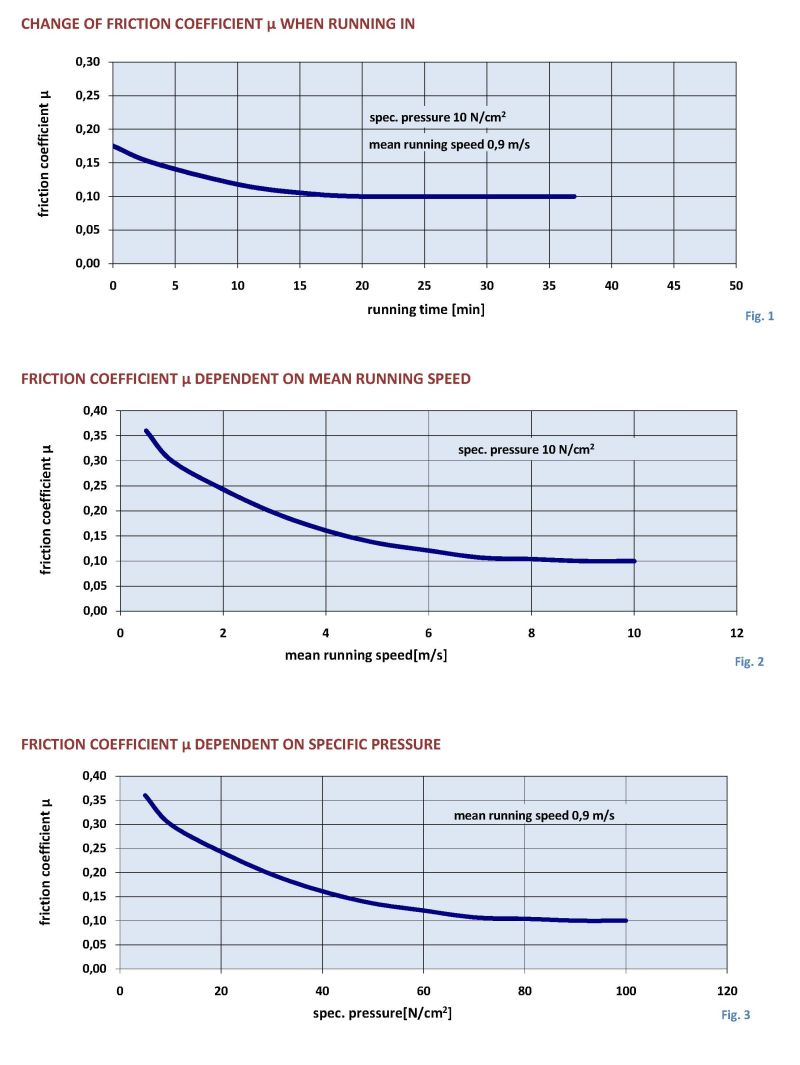
CONSTRUCTION INFORMATION
The good machining properties of graphite give the designer full scope in producing practical designs.
The following guidelines should be observed:
Wall thickness: The choice of wall thickness depends on mechanical aspects. Based on practical operating experience, the graphite bearings should have wall thicknesses which correspond roughly to the empirical equation S = 0.13d + 2.8 ≥ 3 (mm)
Bearing length: To avoid excessive edge pressure and internal stress in the bearing L = d; L ≤ 2d is recommended. The height for washers is recommended as L = 0.1 D • L ≥ 3 (mm).
Flanges: Flange thickness b should be at least as much as wall thickness s (b ≥ s). Flange connections should be radiused and adjoining surfaces machined.
As a general rule: No sharp corners, should be broken or radiused. Shapes should be as simple as possible.
COUNTER FACE MATERIALS
suitable:
- grey cast iron
- plain steel
- alloyed steel (chrome steel)
- hard metal
- ceramic
- glass
suitable under certain conditions:
- nonferrous heavy metal
- chrome nickel steel
- chromium plate materials
unsuitable:
- aluminium and its alloys
SURFACE QUALITY OF THE COUNTER FACE MATERIALS
The surface quality of the counter face materials has an important influence on the durability of carbon and graphite. Counter face surfaces with a maximum surface roughness of Sr <1 μm are recommended. For high pressure lapped and superfinished counter faces with a maximum surface roughness of Sr<0.5 μm are necessary.
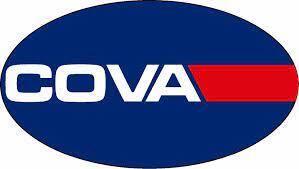