CARBON GRAPHITE
Carbon and graphite linings have a high mechanical strength, great heat resistance, excellent temperature stability and almost universal chemical resistance. In food processing, tasteless and odourless carbon materials are vital to production. Carbon and graphite are particularly useful under difficult chemical and technical conditions where other materials are not suitable. Capable of being machined to fine tolerances, our engineering department ensures that graphite material remains both structurally and dimensionally stable.
WE HAVE THE GRAPHITE SOLUTION FOR YOUR APPLICATION
- Vacuum Furnace insulation
- Inert Gas Furnace Insulation
- Inert Gas Atmosphere Equipment Insulation
- Reaction Vessel Linings
- Bearings
- Segmented Seals
- Piston and Guide Rings
- Mechanical Seals
- Steam Nozzles
- Water Turbine Gland Seals
- Packing Rings
- Contactless Seals
- Vanes
- Sealing Strips
- Stripping components
- Hollow and Container Glass Manufacture
- Flat Glass Production
- Heat Exchangers
- Refractory Systems
INDUSTRIES
- Aerospace Industry
- Aluminium Industry
- Automotive and Mechanical
- Defense Technology
- Electronic
- Glass and Ceramic Industry
- High-Temperature Applications
- Mechanical Engineering Industry
- Metallurgical Industry
- Non-Ferrous Metal Industry
- Recreational Products
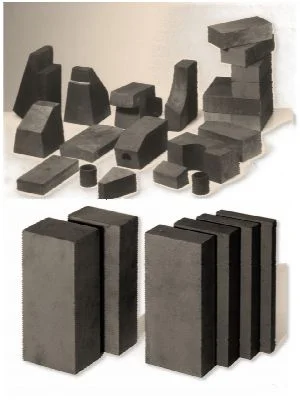
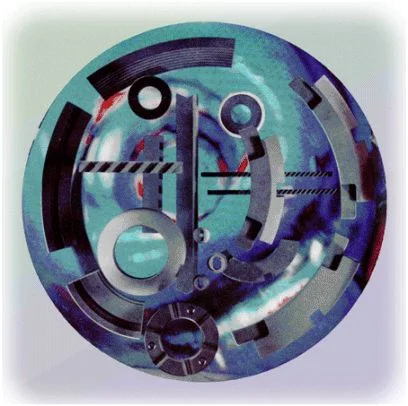
CARBON/GRAPHITE STANDARD BRICKS & SHAPES – FOR CHEMICAL RESISTANT LINING
CARBON/GRAPHITE BEARING AND SEALING – FOR MECHANICAL ENGINEERING
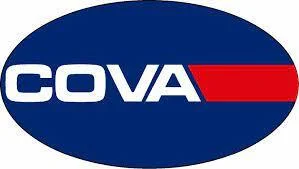