ENGINEERING PLASTICS SELECTION GUIDE
———————————-
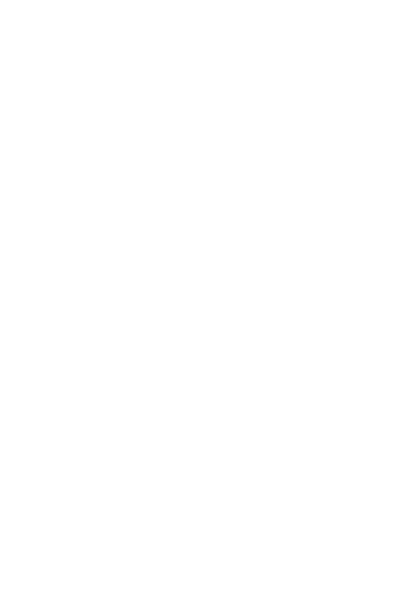
Temperature
Engineering plastics with a continuous maximum operating temperature of 115 degrees celsius or more, are plastics deemed to have high operating temperatures.
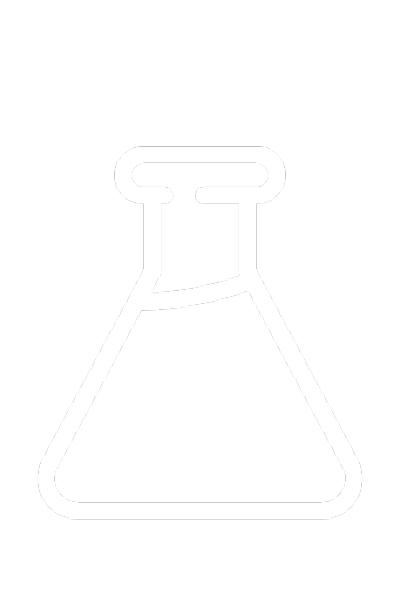
Chemical Resistant
Plastic’s chemical resistivity is ranked on a scale from 1 to 10, where a material with chemical resistance 6 or above is considered proficient.
For more information, contact us.
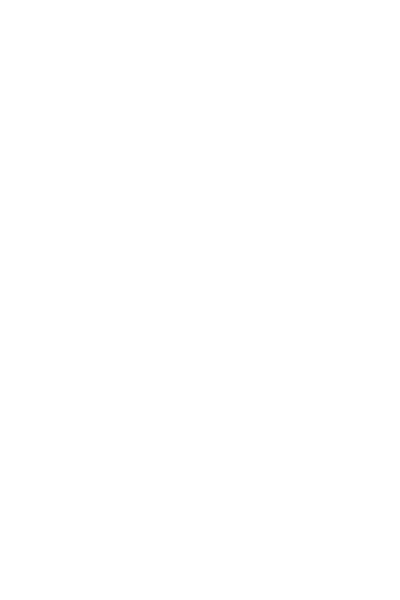
Wear Resistant
Wear resistance is the ability of a plastic to resist the progressive volume from its surface. Plastics rated wear resistance 6 or above on a scale of 10, is deemed to be wear resistant.
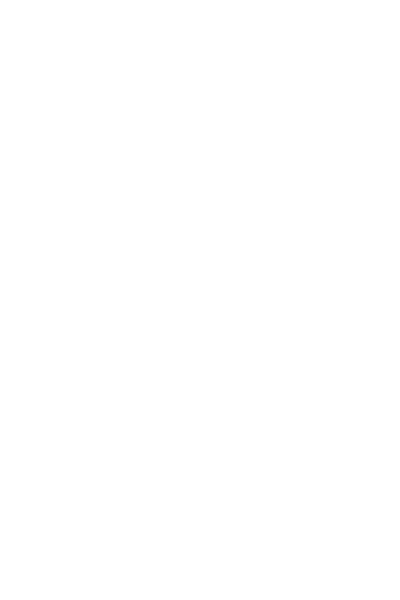
Low Friction
Generally plastics have low coefficient of friction, making them ideal for applications where friction is a consideration. Materials with a coefficient of less than 0.1 is considered to have low friction trait.
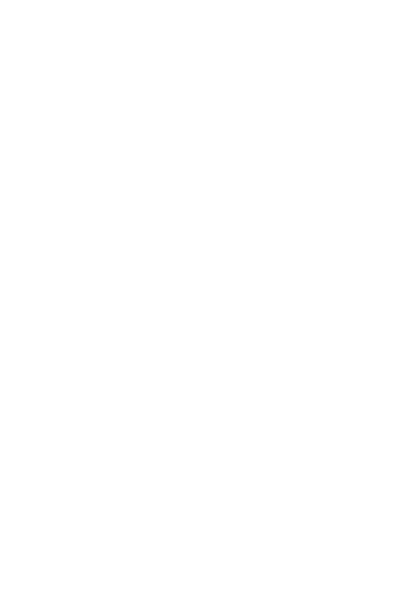
Water Resistant
Water absorption is a material’s capacity to absorb moisture from its environment. A plastic with low water absorption, less than 1% is considered to be adept with water resistance.
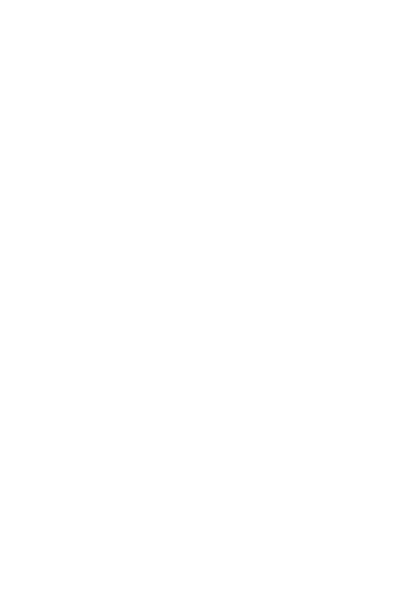
High Dielectric Strength
Engineering plastics can be excellent electrical insulators with thier ability to maintain mechanical properties in high voltage environments. A dielectric strength of 45 KV/mm or greater is adept.
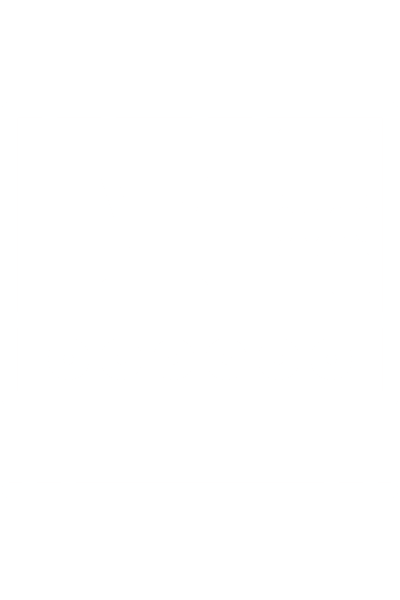
Easy to MachineÂ
Some engineering plastic materials are significantly easier to machine than others. Each plastic is ranked on a scale of 1 to 10 where a machinability of 8 or greater is considered to be easily machinable.
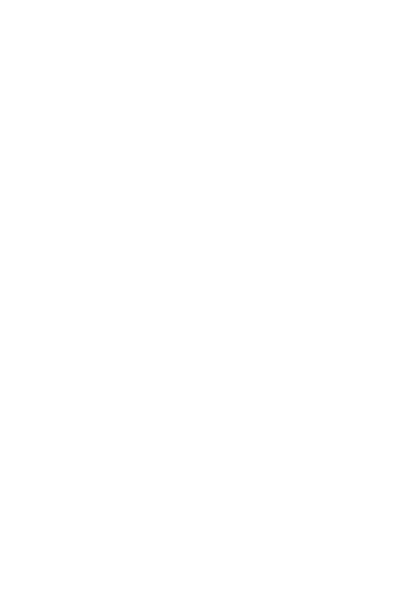
Impact Resistant
Plastics are impact resistant if its able to withstand significant force without structural damage. Each material has a notched strength value, 40 or above to “no break” is considered high impact resistant.
Plastics Selection Guide – Mechanical Properties Comparison
———————————————
Coefficient of Friction
A plastic materials coefficient of friction is its resistance when sliding over another material. Coefficient of friction is the ratio of resistive frictional force divided by the perpendicular force of the two objects pushing together. In the case of most engineering plastics, the friction is between steel, plastic or rubber. Each material is ranked based on their coefficient of friction.
Material | Coefficient of Friction (μ) |
Teflon (PTFE) | 0.09 |
UHMWPE | 0.1 |
Nylon (PA) : T-Glide Wax | 0.1 |
UHMWPE: 9000 GLB | 0.15 |
Nylon (PA) : Natural, Moly, Aquanyl, Impact Resistant, Blue & NGO | 0.19 |
Polyester (PET): Natural & ZX | 0.25 |
HDPE | 0.32 |
Acetal (POM) | 0.35 |
PEEK | 0.38 |
Polyester (PET): SW | 2.5 |
Please note: other properties may affect the performance of engineering plastics in high stress environments.
Wear Resistance
Wear resistance is the ability of a plastic to resist the progressive volume from its surface through actions such as scraping, scratching, rubbing or sliding. This is entirely dependent on the type of contact, environmental conditions and the load applied. To form the below index, abrasion, pin on disk and block on ring tests were taken into account.Â
Material | Wear Resistance (Out of 10) |
PEEK | 10 |
Polyester (PET) | 10 |
Nylon (PA) | 9 |
Acetal (POM) | 7 |
UHMWPE | 6 |
HDPE | 5 |
Teflon (PTFE) | 4 |
Polycarbonate (PC) | 1 |
Please note: other properties may affect the performance of engineering plastics in high stress environments.
Impact Resistance
A materials impact resistance is measured through a notched impact test. Plastics are considered impact resistant if it is able to withstand high levels of force without breaking, fracturing or deforming. A truly tough material is resist this force, able to be ductile and stretch under pressure. Choosing materials with a higher impact resistance can have a significant impact on the life of componentry. Each material is ranked based on a notched impact strength (Charpy) test.
Material | Notched Impact Strength Charpy (KJ/mm^2) |
PEEK | NO BREAK |
UHMWPE | NO BREAK |
HDPE: HD100 Black | NO BREAK |
UHMWPE: 9000 GLB | 130 |
Polycarbonate (PC) | 40 |
Polypropylene (PP) | 30 |
Teflon (PTFE) | 18 |
HDPE | 12 |
Polyester (PET): ZX | 10 |
Acetal (POM) | 6 |
Polyester (PET): Natural | 5 |
Polyester (PET): SW | 2.8 |
Please note: other properties may affect the performance of engineering plastics in high stress environments.
Operating Temperature
The operating temperature of engineering plastics is often separated into two categories: short time (hours) or continuous use (10,000 hours +). Materials are deemed to have reached their maximum operating temperature if there is a significant and consistent decrease in its mechanical properties.
Material | Continuous Operating Temperature (°C) |
PEEK | 260 |
Teflon (PTFE) | 250 |
Polycarbonate (PC) | 115 |
Nylon (PA): HR + UV Stabilised | 115 |
Polyester (PET): Natural & ZX | 115 |
Nylon (PA): Natural, Impact Resistance, T-Glide, Aquanyl & NGO | 110 |
Nylon (PA): Moly + MOS2 | 105 |
Acetal (POM) | 100 |
Polyester (PET): SW Black | 100 |
Polypropylene (PP) | 100 |
UHMWPE | 80 |
HDPE | 80 |
Please note: other properties may affect the performance of engineering plastics in high stress environments.
Material Density
A materials density is calculated by the division of the mass of the material by its volume. The ratio of material density and water density is specific gravity. If the specific gravity is less than 1, the polymer will float when submerged in water. Each material is ranked on their material density (g/cm^3).
Material | Material Density (g/cm^3) |
Teflon (PTFE) | 2.18 |
Acetal (POM) | 1.39 |
Polyester (PET): Natural | 1.38 |
Polyester (PET): SW Black | 1.36 |
PEEK | 1.3 |
Polyester (PET): ZX | 1.27 |
Polycarbonate (PC) | 1.2 |
Nylon (PA): Moly MOS2 | 1.15 |
Nylon (PA): Natural & T-Glide + Wax | 1.141 |
Nylon (PA): Aquanyl CP612 | 1.14 |
Nylon (PA): NGO + Oil | 1.138 |
Nylon (PA): HR Blue + UV Stabliser | 1.135 |
Nylon (PA): Impact Resistant + Plasticiser | 1.11 |
Polypropylene (PP) | 1.03 |
HDPE | 0.955 |
UHMWPE | 0.93 |
Please note: other properties may affect the performance of engineering plastics in high stress environments.
UV Resistance
When selecting the correct engineering plastic material for your application, it is important to consider whether the plastic is UV resistant. Symptoms of plastics effected by UV include: yellowing, leeching, bleaching, stress cracks / brittleness and diminishing strength. Choosing a inherently UV resistant plastic minimises the aforementioned symptoms. Standard plastic may be made UV stable with the addition of additives and stabilisers.Â
Material | UV Resistance (Y / N) |
Acetal (POM): Black | Y |
HDPE: Black, HD100 Black | Y |
UHMWPE: Black, Blue, 9000 GLB | Y |
Polycarbonate (PC) | Y |
Teflon (PTFE) | Y |
Polyester (PET): SW Black | Y |
Nylon (PA): HR Blue + UV Stabliser | Y |
PEEK | Y |
Acetal (POM): Natural | N |
HDPE: Natural | N |
UHMWPE: Natural | N |
Nylon (PA): Natural, Moly, Impact, T-Glide, Aquanyl & NGO | N |
Polyester (PET): Natural, ZX | N |
Polypropylene (PP) | N |
Please note: other properties may affect the performance of engineering plastics in high stress environments.
Chemical Resistance
Although chemical resistance can be simplified, the relationship between corrosive chemicals and plastic materials can be complex with elements such as chemical classification, temperature, wear, time in contact and concentration. For the purposes of a concise resistance matrix, this index will account for the quantity of pure chemicals a material is resistant to in a low stress environment. For more information on specific resistances between plastic materials and acids, contact our sales team. Each material is ranked on a scale of 1 to 10, indexing its suitability in environments requiring high chemical resistance. Each material is ranked on a scale of 1 to 10 – (10 denoting high chemical resistance).
Material | Chemical Resistance (1 to 10) |
Teflon (PTFE) | 10 |
PEEK | 10 |
HDPE | 7 |
UHMWPE | 7 |
Polypropylene (PP) | 7 |
Acetal (POM) | 6 |
Polyester (PET) | 5 |
Nylon (PA) | 4 |
Polycarbonate | 1 |
Please note: other properties may affect the performance of engineering plastics in high stress environments.
Electrical Properties
Engineering plastics can be excellent electrical insulators. Factors that need to be taken into account when assessing a materials electrical properties include volume resistivity, surface resistivity, dielectric strength and the dissipation factor. Materials with excellent electrical properties maintain their mechanical properties in high voltage environments. Each material is ranked on a scale of 1 to 10, indexing its suitability in environments requiring excellent electrical properties. Each material is ranked based on dielectric strength.
Material | Dielectric Strength (KV/mm) |
Polyester (PET): Natural & ZX | 60 |
Teflon (PTFE) | 55 |
UHMWPE | 45 |
HDPE | 45 |
Polypropylene (PP) | 45 |
Acetal (POM) | 40 |
HDPE: HD100 Black | 30 |
Nylon (PA) | 25 |
Polyester (PET): SW Black | 20 |
PEEK | 20 |
Please note: other properties may affect the performance of engineering plastics in high stress environments.
Machinability
Different engineering plastic materials have different ease of machinability. This is mainly caused by low thermal conductivity, low melting points, resist chipping and offer dimensional stability. Important factors in engineering plastic machining:
- Coolants –Â A soluble oil and water solution assists in the prevention of burning material.
- Tooling –Â Sharp cutting edges ensure clean cuts limiting unnecessary friction.
- RPM and Machining Forces – Plastics are required to be machined at lower RPMS and with less clamp force to minimise burning and preventing material deformation.
Each material is ranked on a scale of 1 to 10 – (10 denoting excellent machinability).
Material | Machinability (Out of 10) |
Acetal (POM) | 10 |
Polyester (PET) | 9 |
PEEK | 9 |
Teflon (PTFE) | 8 |
UHMWPE | 7 |
HDPE | 7 |
Nylon (PA) & Polypropylene | 6 |
Please note: other properties may affect the performance of engineering plastics in high stress environments.
Water Absorption
A engineering plastics absorption is its capacity to absorb moisture from its environment. Absorbed moisture acts as a plasticizer, thus reducing the glass transition temperature and the mechanical properties of the material. Each material is ranked on a scale of 1 to 10 – (10 denoting low water absorption).
Material | Water Absorption (Saturated) |
Teflon (PTFE) | 0.01% |
Polypropylene (PP) | 0.01% |
UHMWPE | 0.02% |
HDPE | 0.02% |
Polycarbonate (PC) | 0.36% |
PEEK | 0.5% |
Polyester (PET) | 0.5% |
Acetal (POM) | 0.65% |
Nylon (PA): Aquanyl CP612 | 5% |
Nylon (PA): Impact Resistant + Plasticiser | 5.3% |
Nylon (PA): T-Glide + Wax | 5.9% |
Nylon (PA): NGO + Oil | 6.1% |
Nylon (PA): Moly + MOS2 | 6.3% |
Nylon (PA): Natural & Blue + UV Stabiliser | 7% |
Please note: other properties may affect the performance of engineering plastics in high stress environments.
Tynic’s Engineering Plastics.
Tynic Automation specialises in Engineering Plastics and their applications. With a whole variety of benefits, Engineering Plastics can effectively replace traditional metal or ceramic materials in engineering applications. As polymers often contain a wide variety of compositions and additives, it is crucial to select the correct plastic for your application. The key way to ensure the correct engineering plastic is utilised it to compare the key characteristics needed to be successful in a specific application. These characteristics consist of mechanical, thermal and electrical properties.
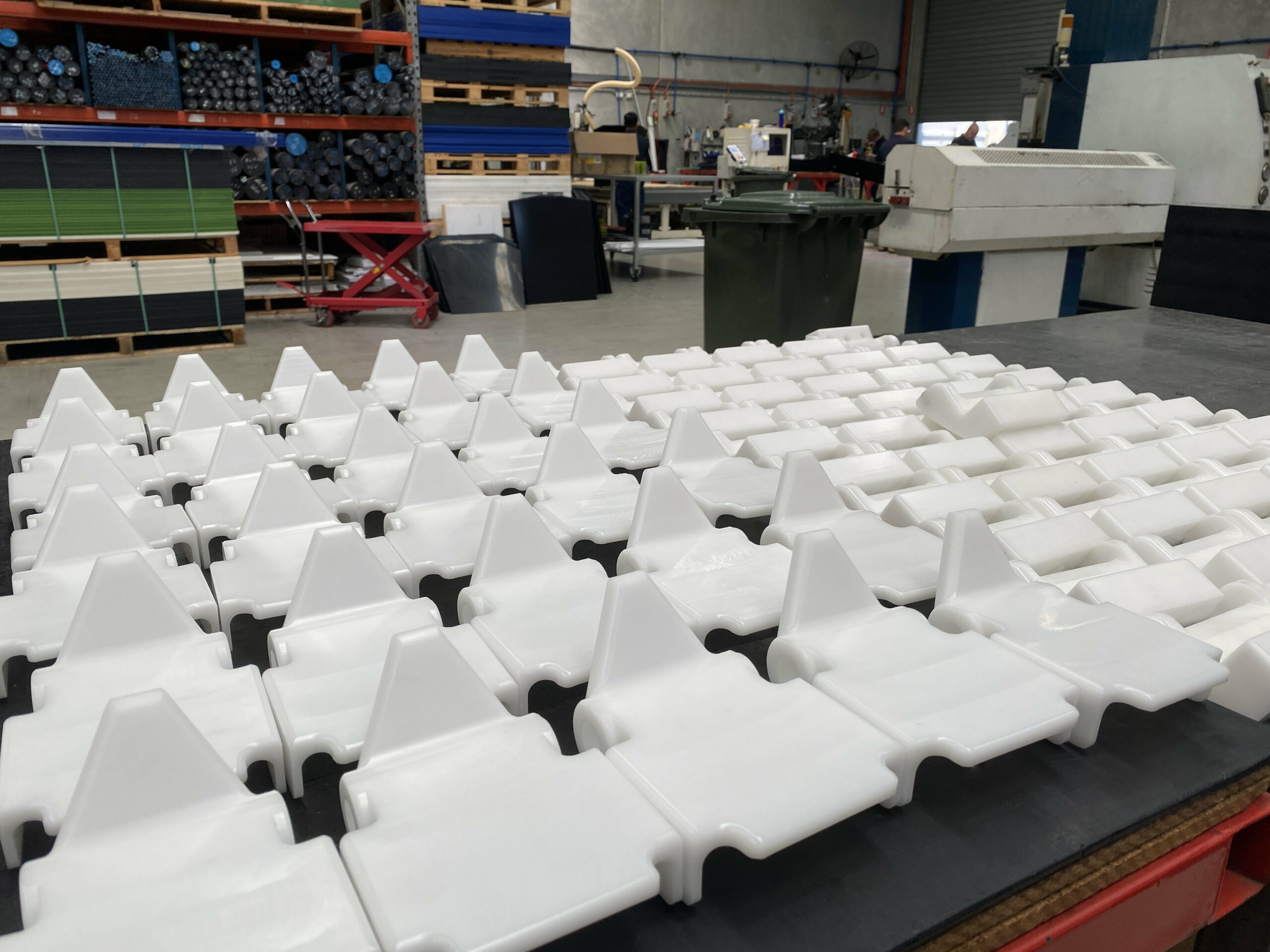
TYNALENE HD300
BLACK
TYNALENE HD300
NATURAL
TYNALENE HD100 (PIPE GRADE)
BLACK
TYNALENE PP
NATURAL
TYNALENE 9000
NATURAL
TYNALENE 9000
BLACK
TYNALENE 9000
BLUE
TYNALENE 9000 GLB
GREEN
TYNALENE 9000 LUBE-X
GREY
TYNACARB
UV2
TYNALON
T-GLIDE
TYNALON
AQUANYL
TYNALON
IMPACT
TYNALON
NATURAL
TYNALON
MOLY
TYNALON
HR BLUE
TYNALON
NGO GREEN
TYNACETAL-C
NATURAL
TYNACETAL-C
BLACK
TYNALYTE
NATURAL
TYNALYTE
ZX GREY
TYNALYTE
SW BLACK
TYNATEF
PTFE NATURAL
TYNAPEEK
BEIGE
TYNAPEEK GF30
BEIGE
G-ETRONAX
EP11 EPOXY GLASS FABRIC
TYNAVIN
PVCU